Equipment Support, Training and Repair Services
At HyFlex, we partner with you to make sure every job is successful.
Equipment Repair
Maintenance Services
Training
Let the HyFlex maintenance team take care of your major maintenance and repairs for you. Our fast turnaround time ensures you'll get your equipment back out on your jobsite quickly. Most repairs can be completed within just a couple days.
-
Repair service
-
Equipment maintenance and tune-ups
-
Rebuilding services
-
Refurbishing service (321E)
Contact us to discuss details.
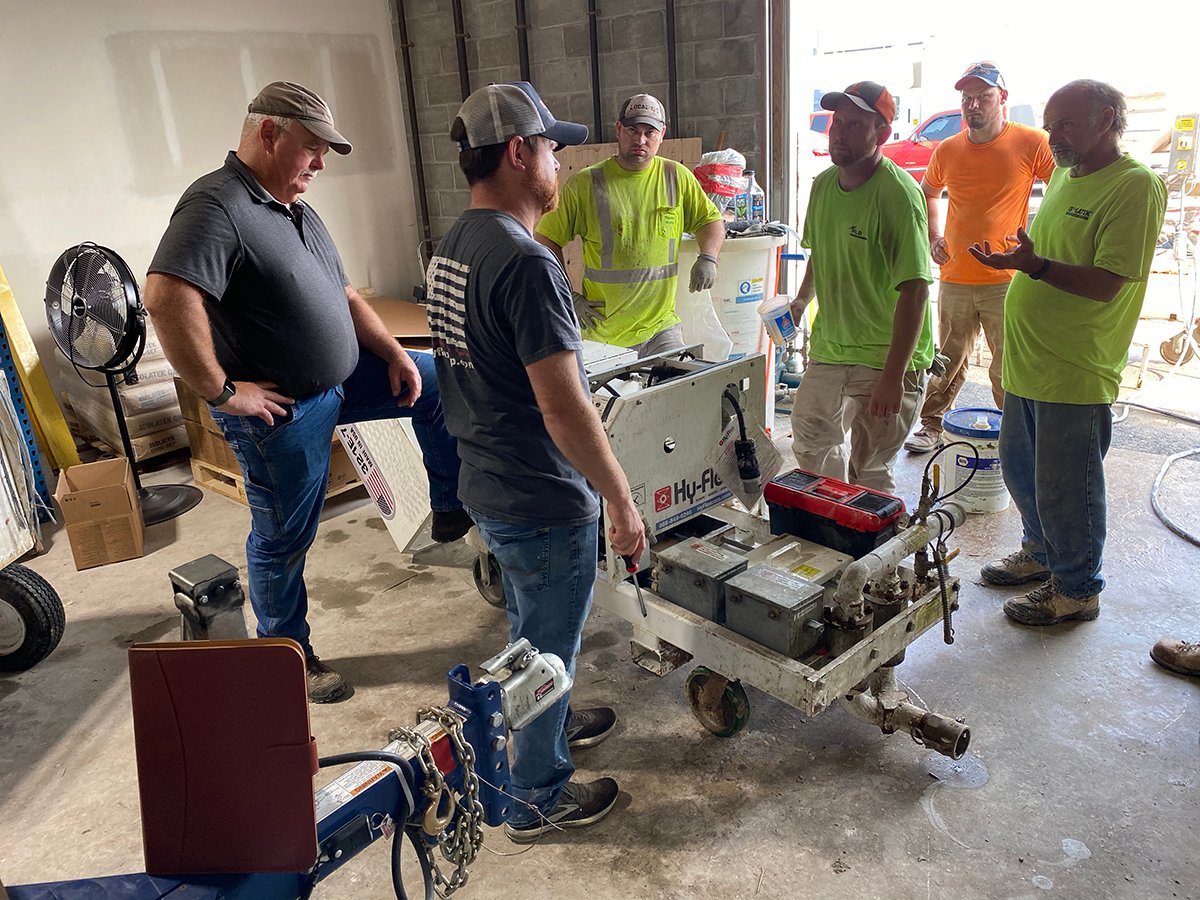
TECHNICAL SUPPORT
888-800-2116
Wherever you need us
Keeping you up and running on the job is our top priority.
If you're not pumping, you're not profiting. That's why our team is here to answer your questions, provide tech support and train your teams to protect your ROI on every project.
Hear what our customers and partners have to say about working with HyFlex and our support team.
Frequently Asked Questions
What are the power requirements for my pump?
This question comes up often, it differs from pump to pump. Please see this chart to determine what power you need:
Patch Pump/Spray Buddy | 115V | 15 full load amps |
RS24E | 208-240V | 20 full load amps |
30E | 208-240V | 30 full load amps |
321E 7.5HP Single Phase | 208-240V | 38 full load amps |
321E Standard | 208-240V 3 phase | 39 full load amps |
321E High Pressure | 208-240V 3 phase | 39 full load amps |
-high voltage units by request only
Please call us for pigtail and cord sizes.How much life can I get out of my pumps wear items?
Each pump has specific parts that wear out over time while being used. Here are some general guidelines to them, due keep in mind this all varies based of material and pressures. A rotor/stator you can expect a minimum of 1000 bags of material with a maximum of 5000 bags. Drive pins should be replaced with every rotor change. On our piston pumps you have parts such as the piston cups which have a minimum of 5000 bags with a maximum of 30,000 bags, as well as the balls and seats which should get you 10,000 - 30,000 bags before change out.
How do I replace a stator tube?
The stator tube change out is a very simple process, but it does have a few tricks to it. Please reference this video we made on how to change one out.
My rotor/stator pump will not push out sponge balls.
If your pump has lost pumping pressure than you will have some worn components. This will either be the stator tube, rotor, or both needing to be replaced.
You can check the pump pressure with a gauge and it needs to read at least 100 psi in order to push the sponge ball.
My drive pins keep breaking on my 30E or Spray Buddy.
If you are constantly breaking drive pins on your rotor/stator pumps that is a good sign of a worn connecting rod or drive shaft. We have replacement parts available on our web store https://shop.hyflexcorp.com/
Why won't my new rotor/stator pump turn?
In storage the pumps can be on the shelf for some time. This can cause the rubber of the stator tube to stick to the rotor. If this happens the pump will not turn. This can easily be fixed by filling the hopper with water and putting the machine in forward and reverse multiple times to un-stick the rotor.
My 321 piston pump is only giving me half production?
There will be an obstruction in the lower intake manifold of the pump. This is due to clumpy material, foreign objects, or dry material. You would need to remove the lower manifold and clear the obstructions. See this video on how to remove the manifold.
Downloadable Resources
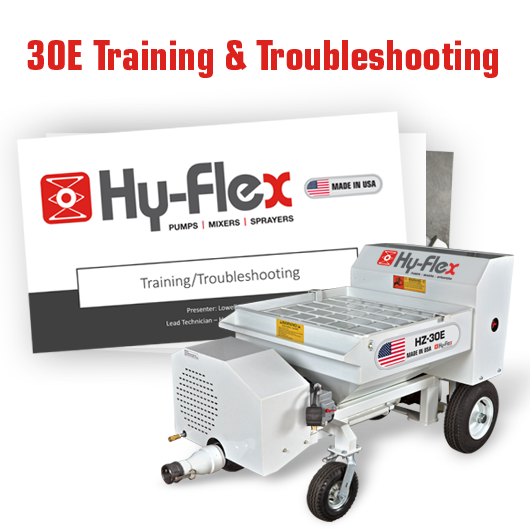
30E Training & Troubleshooting
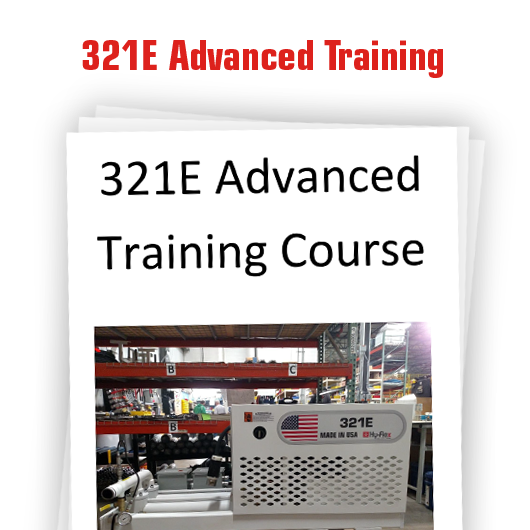
321E Advanced Training Course
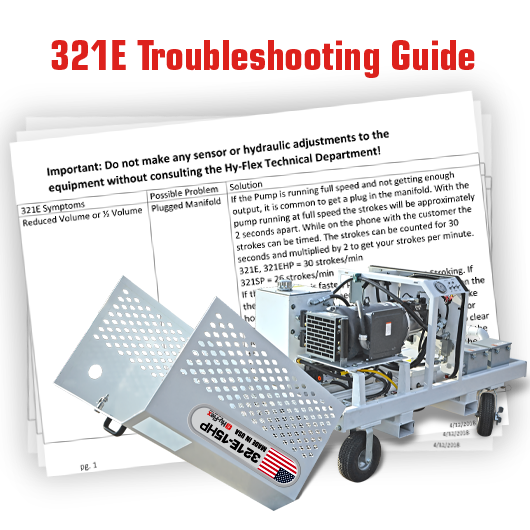
321E Troubleshooting Guide

321E Winterization Procedure
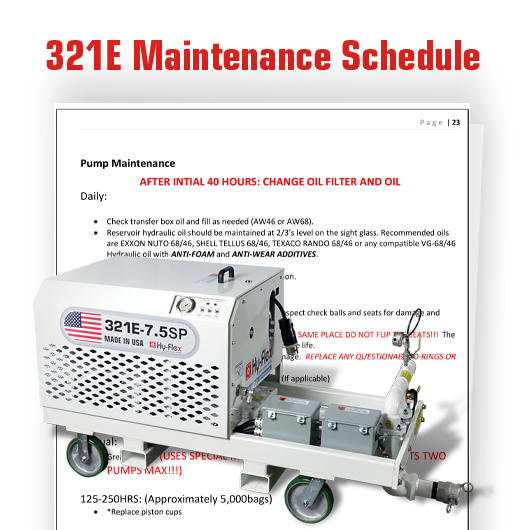
321E Maintenance Schedule
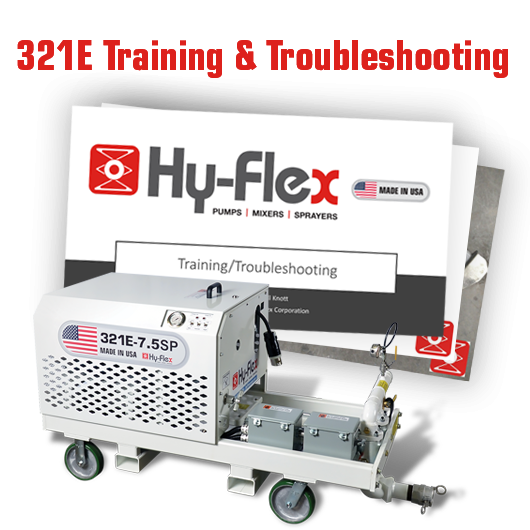
321E Training & Troubleshooting
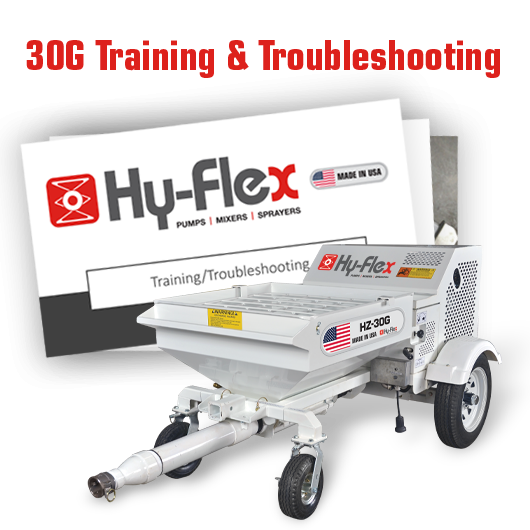
30G Training & Troubleshooting
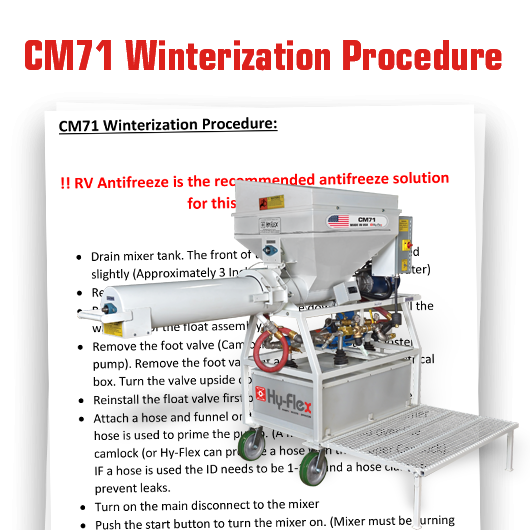